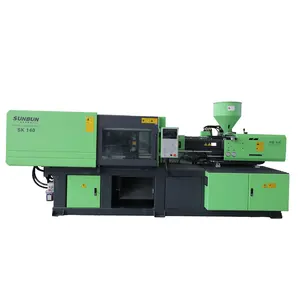
China 140 Ton Small Plastic Injection Moulding Machine Sunbun Desktop Molding Machine Price
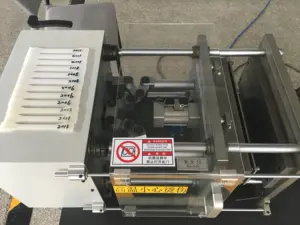
Mold Machine New Electric Lab Horizontal Injection Molding Machine Small Plastic Moulding With Energy-Saving Screw Motor PLc Components


High Precision Custom Mould Maker Plastic Injection Mold Double Color Injection Mould Injection Molding Companies


High Precision Custom Injection Plastic Mold Inject Molding Service Mould Manufacturer


OEM Custom ABS PC PVC Plastic Parts China Molds Plastic Injection Molds Manufacturer

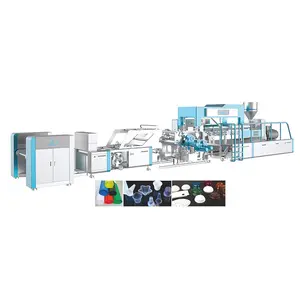
Extruder Machine Price FJL-PC-120-C High Production Profession Plastic Production Line Extruder Pe Extruding Machine


Mini small desktop plastic injection molding machine for small size and laboratory pe

Benchtop Manual Plastic Micro Preform Injection Molding Machine

Haida 50 Ton Mini Small Plastic Injection Molding Machine HDX50 Horizontal Thermoplastic Preform Plastic Making Machine

Wholesale Plastic Manual Bench Model Mini Injection Molding Machine For Making Plastics Parts

Servo energy saving all electric lab benchtop Diy homemade micro small plastic mini desktop injection molding machine

180 Ton China Metal Injection Molding Machine Sunbun SK180 Benchtop Moulding Machine Price

Low Pressure Molding Low Pressure Injection Molding Machine

Mini Desktop Injection Molding Machine Table Top Plastic Injection Molding Machine Automatic Injection Molding Machine

Wholesale Plastic Manual Bench Model Mini Injection Molding Machine for Mini Injection Molding Machine
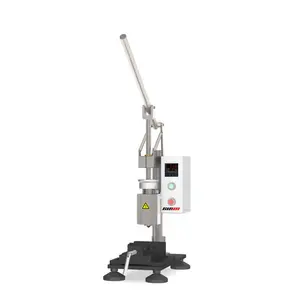
Benchtop Manual Small Plastic Injection Molding Machine

Manufacturer Price Of Horizontal Plastic Bucket Making Machine Injection Molding Machine
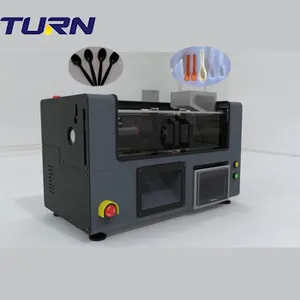
5T laboratory mini Desktop benchtop Injection Molding Machine prototype small run manufacturing machines to work at home
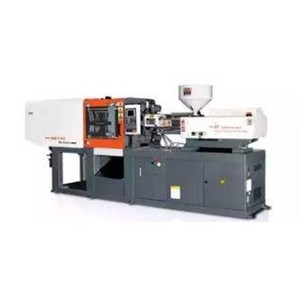
XY2200\B-220tons plastic injection molding machine servo injection molding machinery
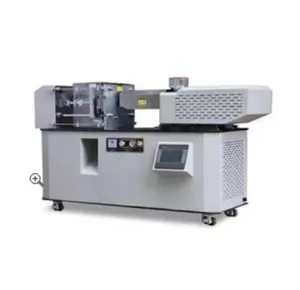
Digg Benchtop Injection Molding Machine
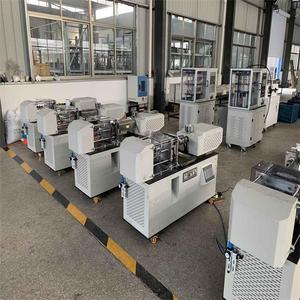
Precision Desktop Injection Molding Machine for lab plastic test

HD130L Mobile Case Injection Machine Benchtop Cell Phone Case Cover TPU Injection Molding Machine Phone Case Making Machine

Factory CE Certificate small manual benchtop plastic injection molding machine Earphone wire injection molding machine

High Quality Desktop Benchtop Manual plastic injection molding machine
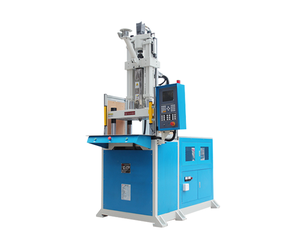
55ton Vertical Injection Molding Machine
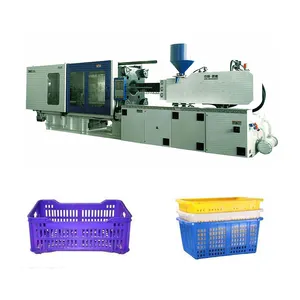
ONGO 550 Ton Plastic Fruit Box Injection Crate Molding Making Machine Small Plastic Injection Molding Machine

LESINTOR Machine Injection Molding Injection Molding Machine Servo Injection 200 Ton Molding Machine
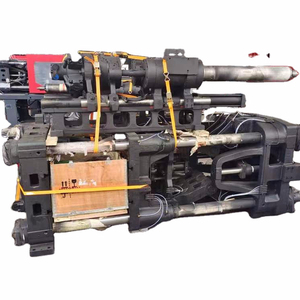
Good Quality Spare Part Horizontal Molding Machine JM-230II Toggle and Injection Unit with plastic injection fixing unit
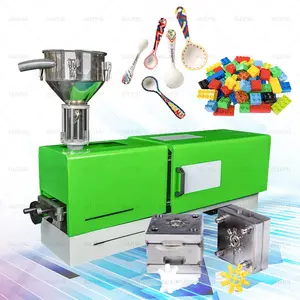
Table Injection Molding Machine Small Scale Injection Molding Machine Desktop small injection molding machine

HM0132 Factory Outlet Bench Table Top Injection Molding Machine Desktop Moulding Machine
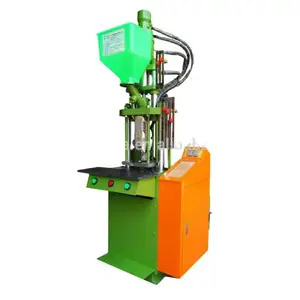
High Quality ABS Cell Phone Case Pet Preform Plastic Automatic Benchtop Car Bumper Injection Molding Machine
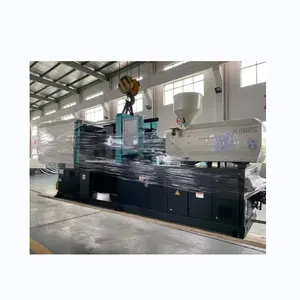
Haijing factory benchtop injection molding machine for sale

Good Quality Horizontal Plastic Product Injection Molding Machine

Hot Selling Good Quality Plastic Injection Machines For Sale Small Plastic Injection Molding Machine

table top plastic injection molding machine
